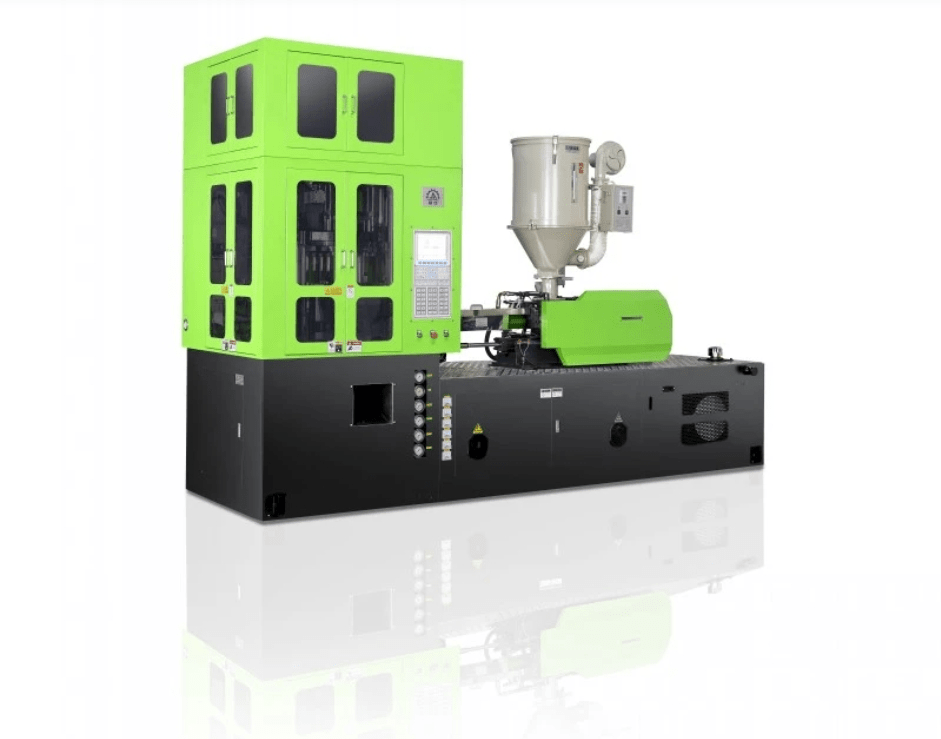
Injection molding machine
Injection molding machine, also known as injection molding machine or injection machine, is the main equipment for injection molding. Its function is to make thermoplastic or thermosetting plastics into plastic products of various shapes using plastic molding molds. Injection molding machine is widely used in mechanical parts,the national defense industry, telecommunications engineering, transportation, instrument industry, electronics and electrical, aviation, ceonstruction, agriculture, medical and daily life and other fields.
The working principle of the injection molding machine is mainly to use the thermophysical properties of the plastic, the material is added from the hopper to the barrel, the material is heated by the heating ring outside the barre, so that the material is melted, and then through the rotation and pushing of the screw, the molten material is injected into the cavity of the mold, after the pressure holding, cooling, curing and shaping, the mold is opened, and the product is pushed out through the ejecting device.
Classification of injection molding machines
The injection molding machine can be classified according to the structural form, which can be divided into horizontal injection molding machine, vertical injection molding machine, Angle injection molding machine and multi-mold rotary injection molding machine.
Horizontal injection molding machine: The mold closing part of the injection molding machine and the injection part are on the same horizontal center line, and the mold is opened in the horizontal direction. Horizontal injection molding machine body is low, easy to operate and maintain; Low center of gravity, stable installation; The product can be automatically dropped by gravity after ejecting, which is easy to realize automatic operation. At present, the injection molding machine on the market mostly uses this form.
Vertical injection molding machine: the closing part and the injection part are on the same vertical center line, and the mold is opened in the vertical direction. Therefore, its footprint is small, it is easy to place inserts, it is convenient to load and unload molds, and the materials falling into the hopper can be plasticized more evenly. However, the product is not easy to fall automatically after ejecting and must be taken off by hand, which is not easy to achieve automatic operation. Vertical injection molding machines should be used for small injection molding machines, generally less than 60 grams of injection molding machines are used more, and large and medium-sized machines should not be used.
Angle injection molding machine: the injection direction and the mold interface are on the same surface, and it is especially suitable for flat products where the processing center part is not allowed to leave gate marks. It occupies a smaller area than the horizontal injection molding machine, but the insert placed in the mold is easy to tilt and fall. This form of the injection molding machine is suitable for small machines.
Multi-mold rotating disc injection molding machine: it is a special multi-station operation injection molding machine, which is characterized by the closing device using a rotating disc structure, the mold rotates around the rotating shaft. This type of injection molding machine gives full play to the plasticizing ability of the injection device, can shorten the production cycle, improve the production capacity of the machine, and is especially suitable for the production of large quantities of products with long cooling and setting time or requiring more auxiliary time due to the placement of inserts. However, because the clamping system is large and complex, the clamping force of the clamping device is often small, so this injection molding machine is widely used in the production of plastic soles and other products.
Analysis of composition and structure of injection molding machine
An injection molding machine is mainly composed of an injection molding system, closing system, hydraulic system, electrical control system and so on
1. Injection molding system: the material is uniformly molded into a melt, and a certain amount of melt is injected into the mold with sufficient pressure and speed.
The injection molding system is mainly composed of plasticizing device (screw, barrel, nozzle, heating ring, etc.), hopper, a metering device, screw transmission device, an injection cylinder, injection seat as a whole moving cylinder
2. Clamping system: Fix the mold, realize the opening and closing action of the mold, and ensure the mold's reliable locking and product ejection during injection molding and pressure holding.
The mold closing system mainly consists of: front setting template, after moving template, tie rod, mold closing cylinder, mold closing device, mold adjusting device, product ejecting device and safety protection device
Electrical control system is mainly composed of: computer and interface circuit, various electrical appliances, detection components, instruments, hydraulic drive amplifier circuit. The organic combination of the two provides power and control for the injection molding machine.
3. Hydraulic transmission and electrical control system: to ensure that the injection molding machine according to the predetermined requirements of the molding process (pressure, temperature, speed, time) and action procedures accurately and effectively.
Hydraulic transmission device is mainly composed of: various hydraulic components, hydraulic control components, hydraulic actuator components and so on
The characteristics of injection molding machine
1. High efficiency: injection molding machine has efficient production capacity. By precisely controlling the melting, injection, pressure holding and cooling processes of plastics, plastic raw materials can be quickly converted into finished products, greatly improving production efficiency.
2. Flexibility: The injection molding machine is adaptable and can handle a variety of different types of plastic materials, such as thermoplastics and thermosetting plastics. In addition, by replacing the mold, it is easy to produce plastic products of different shapes, sizes and designs to meet the diverse needs of the market.
3. Accuracy: Injection molding machine has high molding accuracy. Through the precise control system and advanced injection technology, we can ensure the dimensional stability of the product, the surface is smooth, and meet the strict quality requirements.
4. High degree of automation: Modern injection molding machines are usually equipped with automatic feeding, automatic takeup and automatic detection devices, which realizes the automation of the production process, reduces the dependence on manual operation, and improves production efficiency and product consistency.
5. Energy saving and environmental protection: Injection molding machine pays attention to energy saving and environmental protection in design. Reduce energy consumption and emissions by optimizing heating, cooling and control systems to achieve green production.
6. Easy maintenance: The modular design of the injection molding machine makes maintenance and maintenance more convenient. Each component is easy to disassemble and replace, reducing maintenance time and costs.